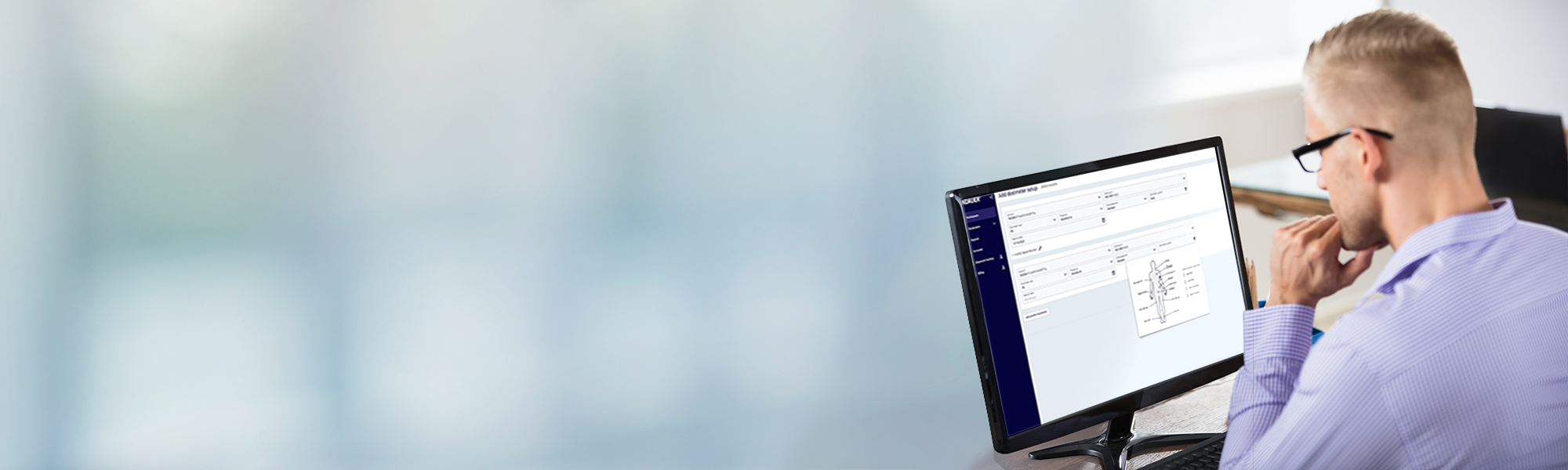
Advanced Topics: Management of Your Personnel Dosimetry Program
Your Radiation Protection Program (RPP) is in place, so what happens next? There are clear steps a Radiation Safety Officer (RSO) or an Individual responsible for Radiation Protection (IRRP) can take to ensure the program stays in compliance with national and state regulations.
Your institution has a comprehensive Radiation Protection Program (RPP) in place. Your Radiation Safety Officer (RSO) or the Individual Responsible for Radiation Protection (IRRP) has determined the necessary equipment needed: Personal Protection Equipment (PPE) to protect employees from occupational radiation, and personal dosimeters, area dosimeters, etc. to monitor radiation exposure. So, what must happen next to keep the plan compliant? This article discusses how RSOs and IRRPs must continue to diligently follow national and state regulations, adhere to ALARA (As Low As Reasonably Achievable) principles, and keep accurate records of individuals’ radiation exposure. There are actionable items and auxiliary steps the RSO/IRRP can take to keep the program compliant.
If this is your first time managing a dosimetry program, or you have questions about some of the basics, you may also wish to read “The Basics of Managing a Dosimetry Program.”
Actionable Items/Atypical Steps
- ALARA 1 AND ALARA 2 Reports
- Minimal (M”) exposures
- Amending Dose of Record
- Discovery of Lost Dosimeters
- Emergency Processing
- Terminate Fetal Exposure Monitoring
- Multiple employers
RSO/IRRP Expectations
- Dosimetry Reports
- Notification of Annual Exposure
- Exposure History Requests
- Annual Review of RPP
ALARA 1 AND ALARA 2 Reports
Every RPP at the minimum must follow the ALARA Safety Principles of Time, Distance, and Shielding. Once those are in place, the plan will address ALARA 1 and ALARA 2 levels specific to the institution’s program. The RSO / IRRP will review their institution’s radiation usage and set goals for what are reasonable amounts of exposure to expect. Then, they will monitor occupational exposure to achieve those goals. Actions are required to be taken if or when those goals are reached or exceeded.
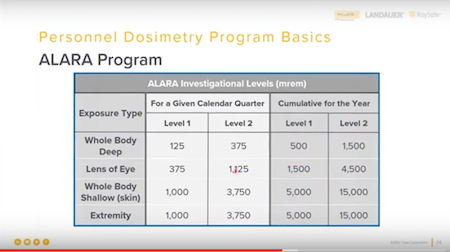
The ALARA Investigational Levels (mrem) table is a great starting point for monitoring exposure. However, the table should be considered default levels, and each institution’s acceptable levels should reflect the radiation environment and workload. If the levels are too low, then employees could constantly exceed them. If the levels are too high, no one’s exposure is accurately captured. No inspector expects to see 0 employees on the ALARA list. Therefore, it is essential to confirm the levels in your program and what clear actions you are committed to taking when individual radiation exposure exceeds those levels.
Let’s go through an example using the table above. In Level 1, in a calendar quarter for whole body deep, the exposure is 125 mrem which equals the 5000 mrem annual exposure limit, divided by quarters (1,250 mrem) and then 10% of that (125 mrem). Level 2 is 30% of the quarter limit. If an individual’s exposure exceeds these levels, these are the suggested actions to take.
Level 1:
- Provide written notification to the individual to make them aware of the exposure.
- Provide the monitoring information.
Level 2:
- Notify the employee in writing about the higher level of exposure, and additionally, an investigation regarding the cause of exposure is launched. The individual is either given a questionnaire to complete or has a face-to-face interview with the RSO/IRRP. It is also common to see a combination of the two.
- The correction actions could include the RSO reviewing the individual’s work habits, reinforcing that the proper PPE was worn, and confirming that the dosimeter was worn correctly (or at all) or wasn’t misplaced, incorrectly stored, or exposed to other radiation sources (e.g. from a medical procedure where the employee was the patient).
- Sometimes there isn’t an apparent reason for high exposure and, that’s OK. The point is for the RSO to pay attention to the reports and the individuals who consistently exceed ALARA 2 and offer corrective actions to reduce those exposures.
- The investigation is documented thoroughly and the participant signs and dates the form. Forward the documentation to the RSO/IRRP and the Radiation Safety Committee (if your institution has one) to keep everyone informed
Level 1 and 2 reports and other documentation should be archived and available for inspection. There are no regulations as to the content or format of the reports but, through our portal, MyLDR.com, LANDAUER customers have access to concise, straightforward ALARA Level 1 and Level 2 sample report forms and questionnaires. The portal generates individual ALARA 1 and 2 reports for each individual for clients to use in their programs.
Much of the focus is on high exposures in ALARA programs and rightfully so. However, attention also needs to be paid to minimal exposure. Recent trends noticed by NRC inspectors are outlined in “Information Notice 2021 02”. The Notice provides insight into findings highlighted during inspections. While medical licensees have programs documenting high levels of exposure, they don’t have any way to trigger low exposure. Minimal (“M”) and very low exposure could indicate dosimeters are not being worn or worn correctly. While there are no requirements for tracking low exposure incidents, it is important to address them. The Notice states that there is an expectation that low exposure in areas with the potential for high exposure (IR, CATH) be explored. RSOs are wise to be aware of all incidents involving exposure and must insist on staff wearing dosimeters whenever they are exposed to occupational radiation.
Amending the Dose of Record
Why an amendment might be needed:
There may be incidents or occasions when it is appropriate for the dose of record to be amended because the exposure to a dosimeter needs to be adjusted. Some scenarios include:
- An inaccuracy is identified on an original report, and you need to apply an EDE correction.
- The result of an ALARA 2 investigation shows a need to adjust the exposure from a dosimeter to a participant.
- A participant tells you they mistakenly wore their dosimeter while undergoing a medical procedure involving radiation exposure.
Adjustments for individual dosimeters, spare dosimeters assigned to personnel, and changes to wear dates can be made. Wear dates can change depending on circumstances, as a dosimeter can be worn beyond the original date assigned.
How to submit an amendment:
The institution’s account manager must submit a Request for Correction in writing to the Landauer Dosimetry Records Department.
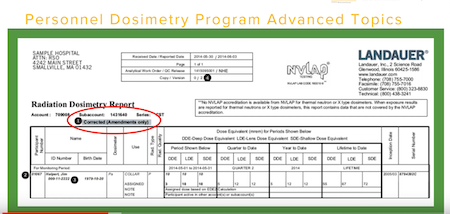
Once a request is received, Landauer will issue a new report with the correction called out. Make sure you receive a copy of the corrected report to add to your files. In the image you can see:
- #1 the word “Corrected” in the red oval
- #2, #3 the participant’s name and the date in bold
- #4 version number, 2
Discovery of Lost Dosimeters
Dosimeters are the property of Landauer, and a replacement fee will be applied to your invoice for any dosimeters not returned. A dosimeter is considered lost if it is longer than 90 days from the end date of the last wear period. If the dosimeter is returned in fewer than 90 days, the fee is credited back to you. If a lost dosimeter is found, you should consider two questions before returning it:
- Where was it found? In a radiation area? On the floor of an imaging room? Was it clipped to shielding PPE that was not being worn by the employee? Or was it found in a non-radiation area (drawer, locker)?
- How long after the end of wear date was it found? Using three months from the end of the wear period as a guideline:
- If found earlier than three months, consider returning it to LANDAUER for processing. Keep an eye on the result and ensure it’s consistent with the history of that participant.
- If found after three months, return to Landauer and mark it “Do Not Process”. However, for accurate record keeping and to prevent a gap in the participant’s history, it is acceptable for you to estimate a dose and assign it to that participant using their work habits and historical data (averaged) to determine the dose.
- The estimated dose record is done in writing, the same as an Amended record.
- Life happens, and dosimeters get lost, but it could reflect poorly on your RPP with an inspector if several wear periods with estimated doses are assigned.
Emergency Processing
There could be times when you need to have a dosimeter processed quickly. For example, perhaps you suspect a situation with very high exposure, or maybe a participant has exceeded the annual limit of radiation exposure. With Landauer, you can overnight a dosimeter where it will be treated with high priority and be processed the same day. Call the Customer Service team to notify them of the emergency, provide the salient information, package the dosimeter and include the pertinent information inside, and clearly mark the outside with “Emergency Processing”. If the dosimeter is received by 10:00 AM CT, you will have results by 4:30 PM that same day. There is a fee for this service.
Fetal Dosimeter
Fetal dosimeters are handled a little bit differently than regular dosimeters. When it is time to stop the fetal dosimeter monitoring, two steps must be taken when returning a fetal monitor.
- Terminate the fetal monitor
- Provide the pregnancy end date; if this date isn’t provided, the fetal dose monitoring will continue past the end date
The fetal dose will be calculated from the assigned whole-body dosimeter and will continue to be monitored until both steps are completed.
Multiple Employers
It is not unusual for a radiation employee to work for more than one employer. Therefore, managing dosimeter compliance becomes a bit more complicated. The annual occupational limits include all sources (radioactive materials, machine produced) and all employers. In a perfect world, that exposure would be shared among the facilities. But some participants are reluctant to share that they work for multiple employers, so compliance is challenging. It relies on the participant disclosing the information to you. There are two strategies you can use in an attempt to get full transparency of the participant’s total exposure.
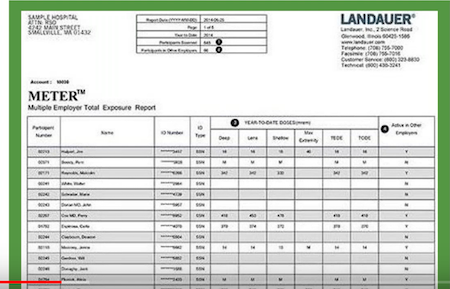
- Reinforce the need to know about other employers at the required annual radiation training. Emphasize that for their safety, they should disclose to you any other facility that monitors their exposure and ensure they are not exceeding the annual occupational limit. Documentation showing your communications with the participant will demonstrate your attempt at compliance with the inspectors. On a quarterly basis, you can share the information with other facilities.
If the other employers are Landauer customers, you can use the Multiple Employer Total Exposure Report, which summarizes the exposure the participant received at different facilities.
Responsibilities and Expectations of the RSO and IRR
Dosimetry Reports
The reports are reviewed on a timely basis depending on the timelines set by your regulatory agency. Signing the reports after review is an excellent way to demonstrate compliance and shows that the reports were indeed reviewed. If you look at the reports and assess them for ALARA 1 and ALARA 2 incidents, you should review them at least quarterly. Once reviewed, archive all the documentation. The reports should be readily available and accessible for inspection. All documentation needs to be kept for the lifetime of the radioactive materials license or the X-ray registration.
Information Included in a Dosimetry Report
The reports are usually available on MyLDR about five days after LANDAUER receives the dosimeters. There is a great deal of important information included in the report:
Click to enlarge - Facility account number
- Wear period dates
- Names of the participants and their identifying numbers/data
- Type of Dosimeter used
- Dosimeter serial number
- Current period data plus summation for quarter/year/lifetime data
- The most significant data: dose equivalents (deep, lens, and shallow) and exposure expressed in mrem
The last page of the report has an in-depth explanation of the abbreviations and their meanings. It’s an excellent reference if you are unsure of the information on the report.
Exposure History Reports
History requests come into play with new employees or when someone terminates their employment. You need to know how much radiation the new employee has absorbed elsewhere before your hire date. Your responsibility is to be aware and informed about their previous exposure so that the former and the current exposure does not exceed the annual limit. You may also receive a history request from another facility. The more common NRC Form 5T is the acceptable format for requesting history and must be signed. NRC Form 4 is used less often and includes the cumulative occupational radiation history, called “planned special exposure”. Once you receive the previous history, you can submit that to the Landauer Records Department to be added to your current account.
Suppose you cannot acquire a complete record of the employee’s current and past exposure. In that case, the NRC guides you to assume the allowable dose limit is reduced by one-quarter of the annual limit, 1.25 rem, for every quarter for which no records were available.
Notification of Annual Exposure
A record of an individual’s annual exposure is provided using the NRC Form 5A if:
- The individual’s annual occupational dose exceeded 100 mrem TEDE, or
- 100 mrem to any individual organ or tissue, or
- The individual requests their annual report
Annual Review of Radiation Protection Program
There are two significant components to the annual review of your RPP
- Content: management and review of the procedures and policies
- Implementation, specific to the ALARA program
- Are the ALARA levels appropriate?
- Is there adequate evaluation of radiation exposure of the staff?
- Are the evaluations and inspections effective in keeping exposure to below ALARA levels?
It is acceptable to make changes to your RPP but be aware that they may require a license amendment. Changes to the RPP need to be documented, archived, and kept for five years. The provisions in your RPP exist for the life of the license or registration. Plus, audits or reviews of the RPP must be documented and kept for three years.
It is important to note that the personnel dosimetry program, the ALARA program, and the annual review of the RPP are always touchpoints for the inspectors. On every visit they make, they are going to be looking at this program. They will inspect the ALARA 1 and 2 reports and review the corrective actions. Were they effective? Are your actions compliant with the commitment you made in the policy? Are you effectively monitoring fetal exposure? Are you reviewing your RPP annually? These actions need to be documented, archived, and available for inspection.
No matter the size of your facility, having a robust RPP that carefully manages dosimeter use, ALARA principles, and accurate reporting will help keep your institution up to date and in compliance with national and state regulations. By following these advanced processes, you can rest assured that you are doing all that you can to keep your employees safe and occupational radiation to acceptable levels.